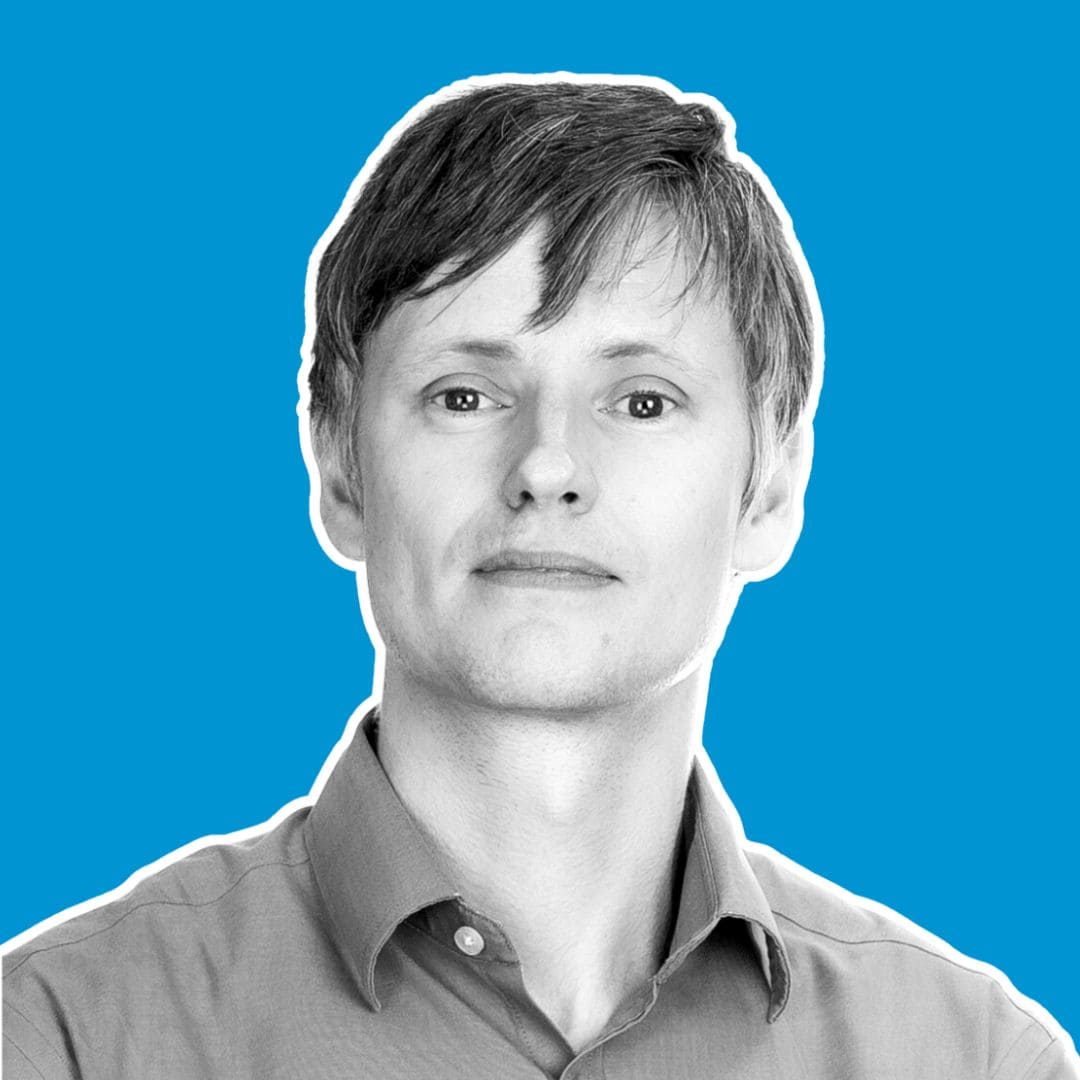
By
Rob Boyle
September 19, 2019
Updated
November 20, 2024
What are some best practices to avoid work site hazards?
Different types of hazards with varying degrees of severity can occur at any work site.
Following these best practices can help you prevent and avoid hazards and prepare for them if they do occur.
Before starting work, take a few moments to evaluate the work area and work activity for potential hazards and discuss their controls.
- Maintain good housekeeping standards
- Inspect tools and equipment prior to use
- Maintain personal protective equipment (PPE) as per the manufacturer’s specifications
- Follow established procedures - do not take any shortcuts
- Report hazards and incidents as soon as possible
By following these guidelines, you can take a very positive step towards the most important thing - going home safe at the end of each day to our families, friends, and loved ones.
What is a Job Hazard Analysis and why is it important?
One of the best tools to come along in work place safety is the Job Hazard Analysis (JHA). This tool makes everyone stop and think about the different risks associated with the task.
Crews must normally gather and write out the JHA before doing a job. This exercise greatly reduces the number and severity of injuries where it is done.
Why should I use a Job Hazard Analysis?
When conducting a Job Hazard Analysis, you may need to take a fresh look at the way things are done at your workplace.
Even though you may hear
“We’ve been doing it that way for 20 years and nothing happened”
it doesn’t mean that a hazard doesn’t exist.
You should take a comprehensive look at all possible hazards with an open mind. Performing a JHA is one of the best methods to develop safe work procedures for any job and operating equipment.
What is "Four Seconds to Safety"?
Job Hazard Analysis can also be used to train employees in the hazards associated with task and what control measures should be practiced. The same principle of these risk assessments can be done nearly anywhere. Simply take a four-second “reset.”
Taking four seconds before starting a new a task has been shown to reduce the probability of an incident by more than 90% versus not taking the four seconds.
You may have done the task you are about to perform thousands of times before. In your mind, you know that you could do it with your eyes closed. It is usually not the task itself but some small thing you did not anticipate that causes the incident.
You did not notice the debris in front of the tool you were going to pick up. You did not notice somebody placed something on the part you were about to pick up. You did not realize how heavy a piece was that you were asked to help carry.
When getting into a vehicle, take a quick look at your surroundings. Change your thinking from where you are going to focusing on the area, road conditions, and other vehicles around you. “Reset” your frame of mind, and by getting in this habit, you will significantly reduce your chances of injury.
Four seconds is all it takes. If you are taking chances or simply moving from job to job, you will eventually get injured.
Get in the habit of taking four seconds and you will significantly reduce your chance of injury while greatly increasing your chances of an injury free day, week, month, and career.