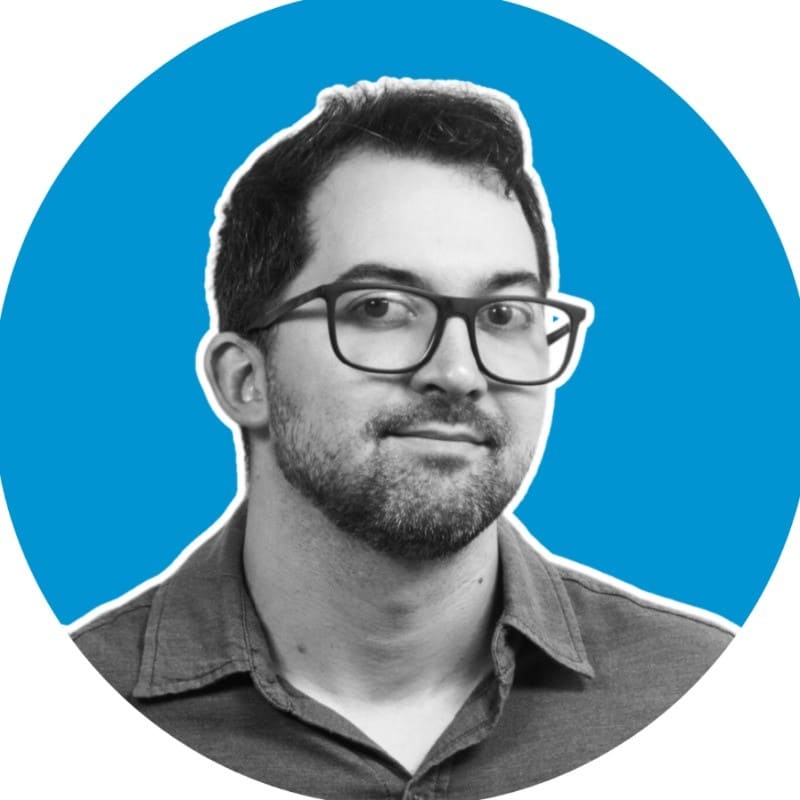
By
Raphael Santos
December 21, 2022
Updated
September 12, 2023
Source: Frame Stock Footage/Shutterstock
Tech is reshaping an established sector and bridging innovations in the energy industry
The world of manufacturing has changed dramatically over the past few years, with technology transforming everything from production to logistics. The rise of the internet of things (IoT) and other innovations has revolutionised the way we do business.
In this article, we look at what digital transformation means for manufacturers and how they can use new concepts like machine learning and datafication to improve their operations.
- What are the 4 main areas of digital transformation?
Business Model Transformation
Domain Transformation
Cultural Transformation
Process Transformation - What is preventing digital transformation in companies?
- Why is digital transformation a challenge for manufacturing firms?
Skills Gap
Adoption of new technologies
Change Management Process
Innovation Policies and Procedures - What is the biggest benefit of digital transformation in manufacturing?
Drives innovation
A more customer-centric approach
Scales up operations - The top 3 trends of digital transformation in manufacturing
Digital Twin
Robotics
Enterprise Resource Planning (ERP) - What are good examples of digital transformation at big companies?
Saipem
SBM Offshore - What is the future of manufacturing technology?
- Why do we need digital transformation in the manufacturing industry?
What are the four main areas of digital transformation?
Digital Transformation encompasses the entire process by which companies interact with customers and employees through the use of technology. This transformation includes four key areas: business model transformation, domain transformation, cultural transformation and process transformation.
Business model transformation
This refers to the change in how businesses operate due to technological advancements. For example, when the first mobile phones were introduced, they were used primarily for making calls. However, today, people use them for sending text messages, taking photos, watching videos, listening to music, playing games and much more.
Digital technologies are allowing companies in the energy industry to also transform their business model. They are using IoT technologies to monitor and control equipment remotely. They are also using predictive analytics to optimise processes and reduce costs.
Source: Frame Stock Footage/Shutterstock
Digital manufacturing requires a connected and agile operations model that is much more sophisticated than traditional manufacturing. They are networked, data-driven, and automated.
Domain transformation
Domain transformation can be associated with digital technologies' capacity to foster new opportunities and generate new markets for companies expanding their core businesses.
For instance, the introduction of Amazon Web Services helped Amazon to play the game of cloud computing by offering a top-notch service. AWS has enabled the giant tech to become the leading provider of cloud services.
We can assume that it’s not necessarily true that every time you transform a business from one type to another, you must be using technology. But it certainly helps and speeds up the process.
Cultural transformation
Cultural transformation is about changing attitudes towards technology within organisations. In the early days of computers, many people feared them because they thought they would take away jobs. Today, however, most people see them as tools that will help them perform better and make their lives easier.
The concept of artificial intelligence as an assistant for employees is how some companies are trying to implement cultural transformation. For example, IBM Watson is being used to provide assistance to doctors who need to diagnose diseases.
And, of course: collaboration, agile methodologies, and a "try-and-error" approach are all good ways to benefit from a mindset shift that comes when we welcome a digital transformation. In other words, embracing a tech culture is also embracing a culture forged with open innovation and experimentation.
Process transformation
In the past, there was no way to know if a product or service was going to succeed before it was launched. Nowadays, thanks to digital technologies, we have access to real-time information about our products and services. We can track customer feedback and measure performance. We can even predict future trends.
Smart factories
Manufacturing is clearly a good example of a sector that is undergoing a process transformation thanks to digitisation and datafication. The rise of Industry 4.0 is helping manufacturers to automate production lines and increase efficiency. It's also enabling them to collect data and analyse it to find out what works best.
This is why we're seeing the emergence of smart factories. These are facilities where machines are connected to each other and to the Internet so they can share information and collaborate. Smart factories allow manufacturers to create value at scale and speed up the development cycle.
Source: Frame Stock Footage/Shutterstock
Digital transformation is also making it possible to develop new products more quickly. Thanks to 3D printing, we can produce prototypes much quicker than ever before. This means that we can test ideas and get feedback much sooner. As a result, we can iterate our designs and launch new products faster.
What is preventing digital transformation in companies?
As a business disruptor digital transformation has its implementation challenges. Firstly, it is not just about technology; it is also about people and processes. Secondly, the change management process can be complex and time-consuming. Thirdly, there are many stakeholders involved in the project.
But whatever your objectives are, make sure that you have a clear vision of what challenges you need to overcome first.
According to a study released by Veeam Software, the "lack of IT staff skills or transformation expertise" is the most common reason why organisations fail to implement digital transformations.
"Dependencies on legacy systems and technology" was another topic highly remembered by respondents together with "still focused on maintaining operations due to pandemic". Veeam listened to more than 3,000 IT leaders for the survey.
This shows how important it is to invest in training your team to be able to support digital transformation initiatives. And it also points out similar challenges in very specific industries and markets.
Why is digital transformation a challenge for manufacturing firms?
Manufacturing is a deeply complex industry. There are many different factors involved when you talk about digital transformation. But certainly, one of the main contributions for us to understand this niche is the article written by researchers Yasser Omar Abdallah (Cranfield University), Essam Shehab (Nazarbayev University) and Ahmed Al-Ashaab (Cranfield University).
Their research created an impressive shortcut for understanding the details of this field by analysing and summarising the current scientific literature on digital transformation within the manufacturing industry.
After selecting several criteria, they developed a framework to answer many questions on the theme, and especially what are the main obstacles to implementing digital transformation in the manufacturing industry.
The group acknowledges those challenges can be divided into four categories: skills gap, adoption of new technologies, change management process, and innovation policies and procedures.
Skills gap
One of the most important issues identified by the authors is the lack of skilled workers in the manufacturing sector, highlighting around "20%-40% skills gap between what is needed and required".
Another issue is the fact that some employees have not been trained properly to handle the new technologies. For example, some manufacturers do not know how to integrate new technologies into their production lines.
The energy industry is closely related to the manufacturing industry because both sectors rely heavily on commodities such as oil and gas. The transition from traditional sources of energy to renewable ones is therefore inevitable for us to achieve net-zero emissions.
The talent needed in a 'greener' economy
We can see offshore wind turbines as a good example of how digital transformation can improve the efficiency of manufacturing this kind of equipment.
As a result, this will greatly impact the talent landscape and the skills needed to keep this green revolution on track. And guess what? Digital transformation has a major role to play in the 'greener' economy.
To anticipate this challenge, we prepared a whitepaper on the theme called "Green Tech Talent Required to Boost Net Zero". The material reunites an in-depth research from scientific papers and reports from top players to delivery a strong evidence about the trends on tech workforce.
Adoption of new technologies
Another obstacle is the difficulty of adopting new technologies. Some manufacturing companies still lack a risk-taking culture to embrace digital transformation more often. In other words, they prefer to stick to low-risk projects with short-term returns.
Cyber-attacks and costs associated with migrating data from older systems to newer ones are other barriers that these organisations face when attempting to implement a digital transformation plan.
Change management process
Another major problem is the lack of a proper change management process. It's normal for people to be resistant to changes, but disruptive technologies are an essential part of digital strategies. So, we need to learn how to deal with them.
And we can forget to mention that implementing these technologies and digitalising manufacturing operations is not a cheap thing.
Innovation policies and procedures
The manufacturing industry needs to take more the first step into innovation. This means that companies should focus more on developing new ideas, rather than just following trends.
They must also invest in R&D activities and encourage creativity among staff members.
What is the biggest benefit of digital transformation in manufacturing?
Drives innovation
As previously stated, a digital transformation strategy helps companies to adopt open source solutions. It can lead the way to the implementation of open innovation, which allows for external knowledge sources to participate in the innovation process.
This makes it possible to generate new ideas and improve existing ones taking into account customer feedback, experts and scholars opinions, competitors and more experts.
A more customer-centric approach
Besides enabling users to interact directly with designers and engineers by providing them with feedback and suggestions, a digital transformation strategy also involves the collection of data about customers' preferences, their behaviour and their needs.
This will help us to understand what people want and how they behave. The end goal is to make sure that we meet their expectations.
Scales up operations
Thanks to the use of big data, digital transformation strategies can be used to optimise processes across an entire factory. They can be applied to any type of business operation, including sales, marketing, logistics, finance, human resources, etc.
For instance, a company could apply a digital transformation strategy to its supply chain management system to ensure that it has enough stock available at all times. Or it could use this same technology to better manage its inventory levels.
In addition to that, these systems can also be used to monitor the quality of products and services, and enables an easier collaboration between departments.
The top 3 trends of digital transformation in manufacturing
Digital transformation is supported by a number of new technologies and methodologies like big analytics, machine learning, cloud computing and internet of things (IoT), but three names are gaining attention recently: digital twin, robotics and enterprise resource planning (ERP).
Digital twin
This technology allows you to create a virtual copy of your physical assets. You can use this tool to monitor the condition of your products and make sure everything is working as expected. It's a great solution for training purposes and simulations.
A digital twin is an effective way to improve the maintenance aspects of a manufacturing company, because it allows its workers to train themselves using the replica and then be prepared for any task they might encounter.
A copy with real-time updates
A key aspect of a digital twin is that you can assume it's an exact copy of the physical asset when you have a real‑time replica, i.e., something which is also numerically identical showing the real-time data about the asset.
This is very important to know, because many digital copies are being mistaken for "twins" when having only the physical aspect replicated. Without the numerical integration showing live data, we can say that we have a digital twin.
Robotics
These machines are used to automate repetitive tasks, such as welding, painting, assembly and packaging. They're also able to perform complex tasks, such as cutting parts out of sheets of metal. It can provide safety procedures and reduce employees burnout.
Enterprise Resource Planning (ERP)
ERP software helps businesses manage all aspects of their business processes and transactions. It includes modules that help track inventory, sales, purchasing, human resources, finance, marketing and customer service.
What are good examples of digital transformation at big companies?
Several organisations are already making progress towards digital transformation. Here are some examples:
Saipem
The Italian multinational services company is one of the most important global offshore energy market players. Saipem has been investing heavily in digitalisation, and its underwater robotics solutions are a tremendous success story of automation of complex inspectional tasks.
Saipem’s autonomous underwater vehicles (AUVs) have been deployed to inspect pipelines and platforms around the world. The company uses AUVs to find leaks, detect corrosion, locate buried pipes and even remove obstructions.
For example, the company developed an advanced underwater drone called FlatFish. The new technology can reduce the carbon footprint by 90% and requires less manpower than traditional methods (almost 70%) of deploying hydrocarbon exploration technologies used today.
The company's most recent endeavours are the ones that have the most to gain from this digital transformation, as they will reach an even more mature phase of Saipem's AI and machine learning capabilities. We can highlight projects like the Fécamps and the Courseulles-sur-Mer offshore wind farms in Normandie (France), in which the company is helping with the design and engineering, supplying the monopile foundations for offshore wind turbines.
SBM Offshore
SBM Offshore has a global and vital role in the manufacturing industry for the energy market. One of its main activities is designing, constructing and operating a vessel, providing solutions across the full product lifecycle.
The company has been leading the charge for digital transformation, having ongoing initiatives backed by datafication and digitisation. All of these digital strategies play an important part in the organisation's offshore business goals by providing us with better service and products.
Being a Floating Production Storage and Offloading (FPSO) provider, SBM Offshore has invested in artificial intelligence tools to detect potential mooring line failures. So, it's no surprise to see its new AI-powered Intelligent Agent Mooring Line Integrity Tool receiving the New Technology Qualification (NTQ) by the American Bureau of Shipping (ABS).
Digital strategies must become transversal between the different areas of a company. SBM Offshore is strengthening its digital portfolio through many innovative solutions, like the 'smart execution' of several projects — the company is digitalising its projects' Engineering, Procurement and Construction (EPC) phases.
What is the future of manufacturing technology?
Manufacturing will continue to evolve over time. The next generation of manufacturing technology may include a strong presence of blockchain and augmentation technologies, such as augmented reality.
Blockchain technology could revolutionise supply chains. Imagine being able to trace the origin of every product back to its source.
Augmented Reality (AR) will become increasingly important in manufacturing. AR headsets will let workers interact directly with real objects, helping them complete tasks faster and more accurately.
And we will no doubt continue to see more robots doing repetitive tasks in manufacturing.
Why do we need digital transformation in the manufacturing industry?
Manufacturing is a very complex industry, which requires high levels of precision and accuracy. This industry has evolved over time, and now faces many technological challenges.
Digitisation and datafication are becoming increasingly necessary because of the rapid development of technology. It will help companies to improve productivity, reduce costs, increase efficiency, enhance customer service and break the boundaries of innovation.
Digital transformation is now the current stage of evolution of manufacturing. So, that is why your company can't delay this change. Possibly, you will need help with your digital transformation, whether by recruiting people with skills capable of leading this process, or outsourcing operations to those who already have this know-how.
Airswift can help you with that and provide a complete package of services from hiring the best talent to global expansion, supporting you on establishing new offices at tech clusters that can influence your process of digital transformation.
We have more than 9,000 contractors and over 60 offices worldwide. Our vast experience within the engineering and technology sectors has helped many organisations set up new hires and other workforce solutions. Take your time to talk to our team and learn more about our services!